Традиционное производство из металлов и пластиков очень расточительно — в авиапромышленности, например, до 90% материалов уходит в отходы. Выход продукции, в некоторых отраслях, составляет не более 30% от использованного материала.
Принтер всемогущий: мультиметаллическая 3D-печать снизит стоимость деталей для российского автопрома
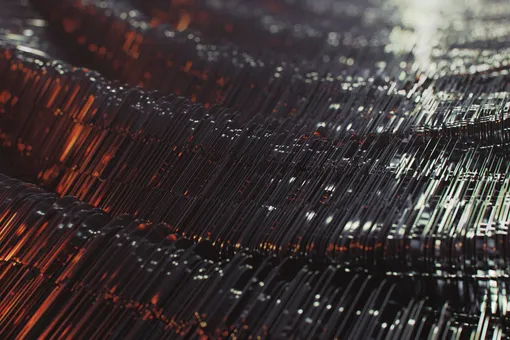
3D-печать металлами потребляет меньше энергии и сокращает количество отходов до минимума. Кроме того, готовое 3D-печатное изделие может быть гораздо легче, по сравнению с фрезерованной или литой деталью.
Одна лишь авиационная промышленность сэкономит миллиарды долларов на топливе — за счет снижения веса конструкций. А ведь прочность и легкость нужны и в других отраслях. Да и экономичность тоже.
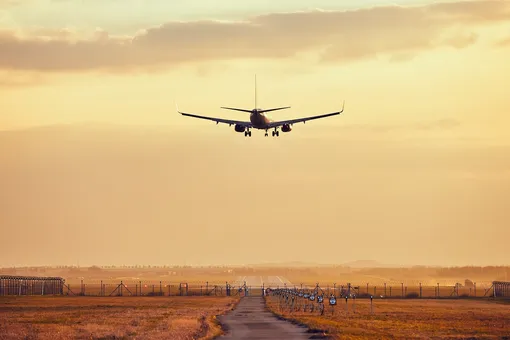
Как научить один принтер печатать разными металлами
Ученые НИТУ «МИСиС» вывели металлическую 3D-печать на новый уровень, представив универсальную технологию производства для различных сфер индустрии на одном 3D-принтере. В качестве основы был взят 3D-принтер российской компании Addsol: его конструкция была оптимизирована и доработана инженерами лаборатории.
Мультиметаллическая печать, предложенная учеными, уникальна, так как позволяет использовать различные, зачастую весьма сложные в обработке, металлы и их сплавы.
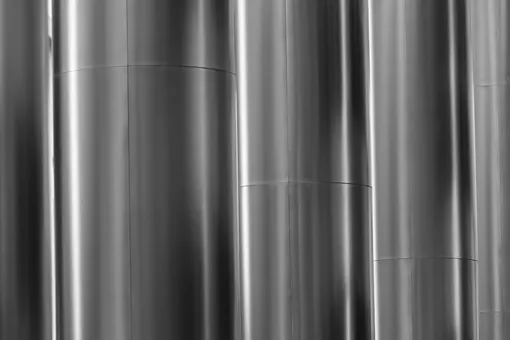
Ученые лаборатории «Катализ и переработка углеводородов» научились печатать 3D-изделия из металлов разных групп на одном принтере. Технология, снижающая себестоимость 3D-изделий в среднем на 30%, позволяет получать как изделия для медицинского применения, так и детали для авиакосмической промышленности.
Для печати одной группой металлов пришлось оптимизировать конструкцию принтера, для печати другой — модифицировать сами материалы при помощи добавок и катализаторов.
Исследователи подчеркивают, что используют несколько подходов.
- Работа с различными распределениями энергии в пятне сплавления.
- Работа с температурными режимами непосредственно на 3D-принтерах.
- Модификация металлопорошковых композиций путем смешивания с добавками (от наноалмазов до углеродных волокон).
В итоге была создана уникальная система селективного лазерного плавления для получения 3D-образцов малых размеров из металлов и сплавов.
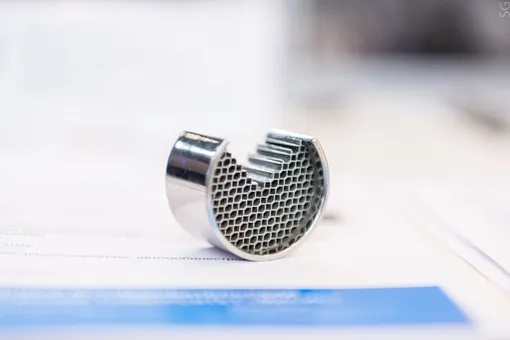
Укрощение материалов
Магниевые сплавы, например, невозможно обрабатывать без использования специальных солевых флюсов, поскольку они воспламеняются и горят. Технология изменила модификацию принтера, подбор режимов и систем обдува, что позволило печатать медицинские изделия из магния — биорезорбируемые зажимы-фиксаторы костных тканей, челюстно-лицевые имплантаты.
Одно из интересных и перспективных применений технологии, по мнению самих разработчиков, — печать постоянных магнитов из порошка неодим-железо-бор. Они применяются для создания генераторов, электродвигателей в автомобильной и авиапромышленности. Производство таких магнитов по традиционным технологиям — это многоступенчатый, дорогостоящий процесс. 3D-печать позволила сократить количество стадий синтеза, уменьшить стоимость самой детали. Кроме того, аддитивное производство дает возможность синтезировать магниты не только в форме диска или параллелепипеда, но и любой другой сложной конфигурации.
В настоящее время коллектив тестирует режимы печати из бронзы и меди, которые могут использоваться для ракетных двигателей, а также из магниевых сплавов и чистого вольфрама.
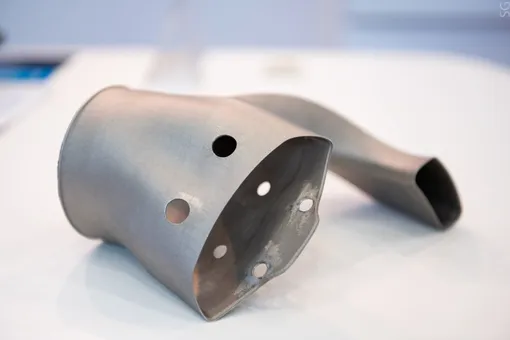
Первые победы: оптимизированные детали для аэрокосмоса
Медицина, авто, авиа-космос, машиностроение – сферы, для которых уже может производить продукцию разработанная 3D-система. В рамках XVII всероссийского форума «ГОСЗАКАЗ» НИТУ «МИСиС» представил ряд готовых деталей для авиакосмоса и автомобилестроения из нержавеющих и цветных сплавов, полностью напечатанных на новом устройстве. Некоторые из них невозможно изготовить традиционными методами. Разработанная учеными технология снизила себестоимость изделий и сократила время производства в среднем на 30-50%.
На форуме были представлены реальные узлы для современного машиностроения с оптимизированными характеристиками:
- Патрубок системы охлаждения, применяющийся в автомобилях, полностью полученный методом селективного лазерного плавления (SLM). Изготовить такую деталь возможно только аддитивным методом, так как толщина стенки изделия — 0,3 мм, у существующих аналогов — 2 мм.
- 3D-печать форсунки гидросбива окалины для металлургических производств позволила оптимизировать конструкцию изделия, сократив количество деталей с шести до одной.
- Пламегаситель, предназначенный для обработки, охлаждения и снижения скорости раскаленных выхлопных газов в авиа- и ракетостроении, специалисты также синтезировали методом SLM.
- Из титанового сплава был произведен востребованный в авиапромышленности теплообменник. Лазерное плавление позволило изготовить деталь за одну технологическую операцию вместо трёх.
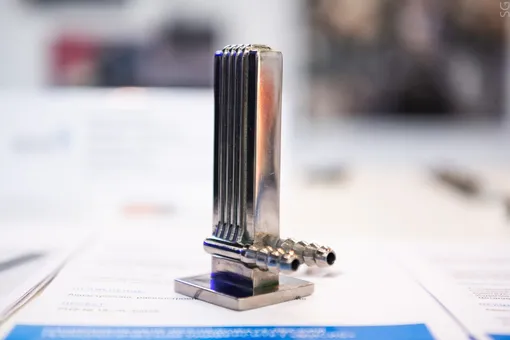
Научный коллектив сходится на мнении: пока нельзя однозначно утверждать, что аддитивные технологии – быстрее, выше, сильнее. Да, можно облегчить деталь, упростить сборку, но себестоимость изделия складывается в том числе и из стоимости сырья, а порошок для печати пока дорогой. Аддитивные технологии – не панацея, но отличное подспорье для более быстрого производства в современных российских реалиях.