В строительстве 3D-принтеры появились не вчера, однако широкого распространения не получили: здесь чаще применялись портальные устройства, которые имеют ряд ограничений.
3D-печать домов, роботы-диагносты, космические двигатели и сверхпрочные ткани: как российские стартапы создают будущее
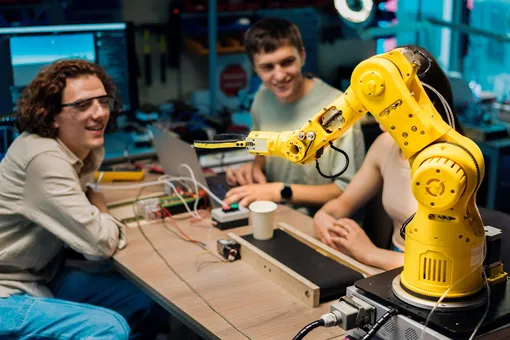
Цементный муравей
Но строительные 3D-принтеры консольного типа могут изменить тенденцию. Одно из первых таких устройств называется CemAnt: cem отсылает к цементу, а ant в переводе с английского означает «муравей». Аппарат может перемещать экструдер в трех измерениях, печатая стены сложной формы, он относительно легкий и весьма мобильный.
Генеральный директор фирмы Максим Канищев объяснил нам, как инженеры компании «Парк3Д» из Выксы пришли к такому решению и каким образом его реализовали.
От металла к бетону
«Мы выросли из кузнечного цеха, — рассказывает Максим. — С 2015 года наша команда производит металлические конструкции для торговых центров и многое другое, в том числе мы создавали городские арт-объекты. И в какой-то момент у нас появилась гениальная, как нам казалось, идея: сделать для изготовления скульптур 3D-принтер, который печатает металлом. Взять сварочный аппарат, посадить на консоль и печатать проволокой — такая технология называется Wire Arc Additive Manufacturing, WAAM. И у нас все получилось.
Сейчас мы таким способом изготавливаем и промышленные конструкции, и арт-объекты — десятки наших скульптур стоят по всей России. Но главное, мы поняли, что 3D-печать металлом — это интересно. А поскольку сложность ее весьма высока — тут и температуры, и окалина — мы неплохо разобрались в механике процесса. Мысль о создании конструкции, печатающей бетоном, появилась самым естественным образом: строители уже несколько лет жалуются на нехватку людей. Но идея создания портального 3D-принтера нас не привлекала. Недостатки таких устройств были очевидны: эти машины тяжелые и громоздкие, их установка может занимать недели, а печатать здания они могут не выше четырех этажей, да и размеры постройки в плане имеют ограничения.
Мы решили сделать маленький принтер, который будет печатать в радиусе 4 м вокруг себя. И легкий, максимум 300 кг, чтобы можно было вручную перекатывать его на колесиках или с помощью подъемного крана перемещать между этажами.
В итоге получившуюся конструкцию легко транспортировать до объекта без разборки, а на ее подготовку к запуску требуется всего час. Или, если речь идет о рое принтеров, не более четырех часов. Кстати, возможность работы роем мы закладывали изначально. Это дает и скорость — этаж за смену — и гибкость в работе».
Смешать, не транспортировать
Важная особенность CemAnt заключается еще и в способности делать смесь непосредственно в экструдере. Это, в частности, решает вопрос быстродействия, ведь перед укладкой следующего слоя бетон должен затвердеть. Присадки, повышающие скорость застывания бетона, известны давно. Но если готовить быстросохнущую смесь заранее, при задержке в работе она может окаменеть прямо в системе подачи. А вот когда бетон замешивают в экструдере, присадки приходятся как нельзя кстати.
Благодаря компактности и мобильности CemAnt удобно использовать для возведения внутренних перегородок. Для подрядчика при блочном строительстве это всегда головная боль: нужно подавать смесь, применять ручной труд. А на рой из нескольких принтеров достаточно одного оператора, запускающего программу со смартфона или планшета.
Еще одна прелесть строительства с 3D-устройством — работа четко по проекту. Что заложено, то и получается. В том числе сложные формы: напечатать полукруглый выступ CemAnt даже проще, чем прямоугольный.
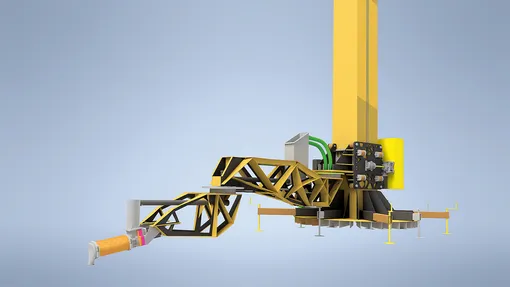
Дом за смену
Проект CemAnt уже получил признание: в 2024 году он стал победителем конкурса мэра Москвы «Новатор Москвы» в номинации «Меняющие реальность». «Мы видим огромный потенциал в этой технологии, — говорит Максим Канищев. — Она не только решает проблему нехватки кадров в отрасли, но и открывает новые возможности для архитектуры и дизайна».
Принтеры CemAnt, как и другую строительную технику, планируют либо продавать, либо сдавать в аренду — ориентировочно это будет стоить 40–50 тысяч рублей в день за единицу. Притом что роем из шести принтеров за восемь часов — одну смену — можно напечатать, например, стены одноэтажного частного дома площадью до 100 кв. м.
Трактор для трубы
Представьте, что вы ползете внутри трубы по остаткам нефтепродуктов, таща за собой тяжеленный блок с диагностическим оборудованием. Двигаться трудно, особенно когда труба поворачивает под прямым углом, но еще сложнее будет возвращаться: развернуться внутри не получится. Представили? Тогда вы понимаете, как хорошо, что для этих целей применяют роботов. Альтернативы им во внутритрубной диагностике практически нет, поэтому мировой рынок таких роботов стремительно развивается, ежегодно прирастая на 20%, и на сегодняшний день достиг уже 2 млрд долларов.
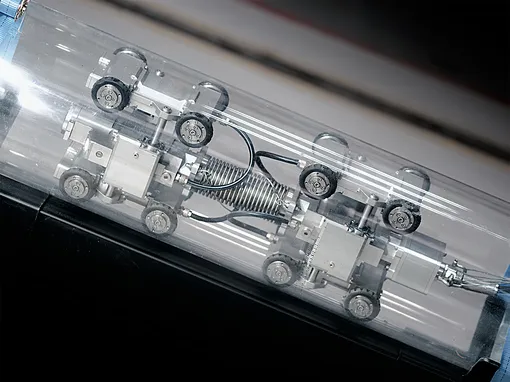
Страна победивших трубопровод
В нашей стране трубопроводов больше, чем дорог: последних, если говорить про опорную сеть, 140 тысяч км, а первых, по разным оценкам, от 270 тысяч до 2 млн км. И вся эта система требует регулярных проверок и ремонтов. Причем, если трубопровод закопан под землю или проложен под водой, это еще полбеды. Но когда он находится под сооружением, провести диагностику иначе, чем с помощью внутритрубных роботов, практически невозможно.
Впрочем, даже когда извлечение трубы не вызывает проблем, для поиска протечек с нее придется снимать защитный кожух (а он может быть, например, бетонным) и изоляцию, которая плохо отходит. Намного эффективнее запустить внутрь самоходное устройство с диагностическим блоком. Такие роботы нужны нефтяникам и газовикам, водоканалам, теплосетям, а также атомной, металлургической, химической и многим другим отраслям промышленности. В том числе для профилактической диагностики, потому что аварии способны нанести ущерб на десятки миллиардов рублей, не говоря уже о риске экологической катастрофы.
А теперь предоставим слово разработчику, Станиславу Розанову.
Защита класса ноль
«Около восьми лет назад один крупный российский оператор магистральных нефтепроводов провел анализ рынка и убедился, что ни одно из существующих устройств по диагностике трубопроводов не соответствует его требованиям на ближайшую перспективу. Ключевым критерием была способность перемещать объемные диагностические модули внутри трубы: чем больше оборудования, тем результативнее исследование.
Второй важный момент — взрывозащита класса ноль. Устройству предстояло работать внутри труб, в которых даже после остановки потока присутствуют нефте- и газосодержащие смеси. Оператор магистральных нефтепроводов обратился к группе «Роснано» с предложением разработать мощного внутритрубного робота, для которого они сами сделают соответствующий диагностический модуль. Специально под эту задачу и организовали наш стартап, впоследствии ставший робототехническим доменом «Роснано», всего здесь сейчас трудится семь человек.
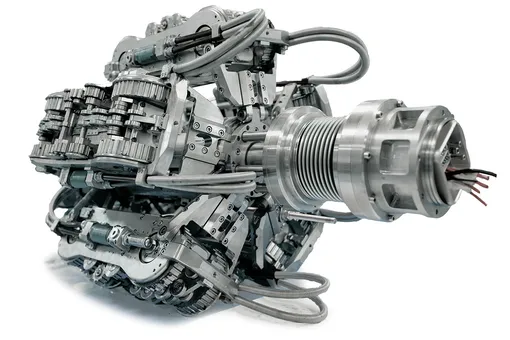
В 2019 году нашим партнером стала немецкая компания, которая занималась роботами уже около 40 лет. Мы вели совместную научно-исследовательскую деятельность и выступали в качестве их представителей в России — в том числе в области продвижения германских роботов с роликовым движителем, способных преодолевать вертикальные повороты в трубе. Увы, вскоре партнеры начали сворачивать сотрудничество. В итоге все НИОКР мы стали вести сами. Результатом нашей работы стал гусеничный робот, который сейчас уже проходит сертификацию. Кроме того, на основе немецкой модели мы сделали и запустили на рынок робота с роликовым движителем, но с нашими усовершенствованиями.
Ключевая особенность нового гусеничного устройства — тяговое усилие в 1000 кг. Этим оно отличается от других внутритрубных роботов, как трактор от легкового автомобиля. Кроме того, у него больше гусениц, большая площадь прилегания.
Второй, не менее важный момент — взрывозащита класса ноль. На российском рынке других таких устройств просто нет, а на мировом — есть, но с более скромными тяговыми характеристиками.
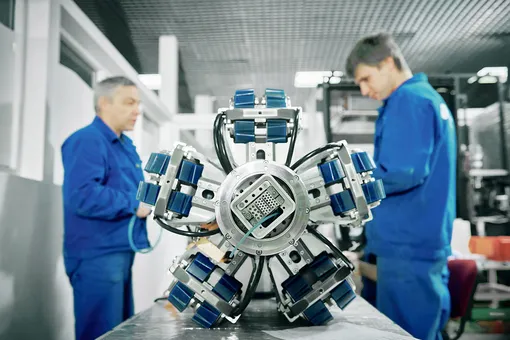
Наш робот состоит из четырех тяговых блоков: два впереди, два сзади, а по середине диагностический модуль, который примагничивается к стенкам трубы. На каждом тяговом блоке по пять гусениц, расположенных по периметру: устройство движется, распираясь внутри трубы.
Управляют роботом по кабелю. По нему же идет вся телеметрия с устройства, подаются энергия и газ, который обеспечивает давление в шасси. Длина кабеля составляет 500 м — таким было техническое задание. Но в принципе провод можно и увеличить. Ну а модульная конструкция робота позволяет ему легко проходить повороты и дает возможность относительно быстро переделывать машину под разные задачи: на робота можно навешивать разные модули для ремонта, очистки и обработки трубы».
Ткань новой реальности
В мире из прочных и легких композитов на основе 3D-ткани делают корпуса беспилотников, гребные винты подлодок и кораблей, лопатки турбин авиадвигателей, детали автомобилей и космических аппаратов, защитные устройства для армии. И это лишь часть длинного списка.
Что такое 3D-ткань? Это объемные переплетения нитей. Пропитав их эпоксидной смолой или другим наполнителем, можно получить материал, который, в отличие от традиционного слоистого композита, не подвержен расслоению при деформационных нагрузках. Он имеет однородную структуру, как металл, что позволяет использовать такую ткань для изготовления силовых элементов.
Забытая технология
Технологию 3D-ткачества придумали еще в XX веке, причем занимались ею и в СССР, и в других развитых странах. Вот только у нас с распадом Союза работы в этой области остановились, а за рубежом нет. Сейчас продукция из 3D-ткани очень востребована, но в России ее производство смогла поставить на поток всего пара компаний. Одна из них сфокусирована на оборонных заказах, а вторая, «Карбонтекс», ориентируется на гражданские нужды. В 2024 году этот проект стал победителем конкурса мэра Москвы «Новатор Москвы» в номинации «Лидеры инноваций» (направление «Промышленность»).
Спасибо санкциям
Возрождение отрасли в стране началось около 10 лет назад, когда в Казанском национальном исследовательском техническом университете им. А. Н. Туполева по инициативе советника ректора Вячеслава Рогожникова открыли лабораторию 3D-ткачества. Лаборатория, которую возглавил кандидат технических наук Петр Белинис, ученик профессора Василия Александровича Гордеева — основателя советской школы 3D-ткачества, занималась научными исследованиями и опытно-конструкторскими разработками. Однако, когда благодаря знаниям Белиниса удалось кустарными методами, буквально из дерева сделать действующий прототип станка, стало понятно: российская технология позволяет производить продукцию, востребованную рынком.
Для коммерциализации изобретений была создана компания «Карбонтекс»; ее научным руководителем стал Петр Белинис, а генеральным директором — Вячеслав Рогожников. Команда на собственные средства спроектировала и собрала свой первый полноценный ткацкий 3D-станок КТ-6250 («КТ» означает «комплекс ткацкий», а число 6250 — сечение зева в миллиметрах). Устройство получилось тихоходным, зато с широким диапазоном регулировок. Оно отлично подходило для отработки технологии, но для производства требовался другой станок, побыстрее.
Внешне КТ-1000 похож на обычный ткацкий станок. Но при внимательном изучении видно, что механизм управления нитями устроен совсем по-другому. Одни нити поднимаются, другие заходят под них, в итоге получается нечто похожее на тканый пирог.
В базовом варианте нити идут в трех направлениях — параллельно координатным осям, но можно добавить еще два, меняя рисунок переплетения. Одновременно в процессе может быть задействовано до 10 тысяч нитей из разных материалов: на углеродной основе, из стекловолокна или арамида. Кроме того, технология позволяет комбинировать нити нескольких типов, локально изменяя свойства преформы.
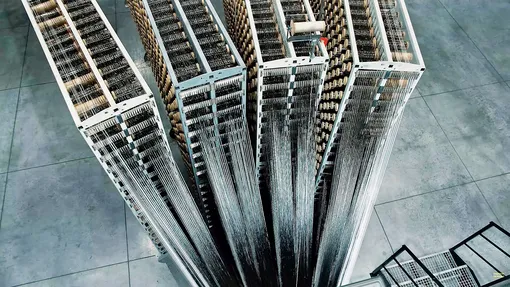
Точность дается не всем
Наш собеседник особо подчеркнул, что при производстве изделий из 3D-ткани требуется максимальное приближение к конечной форме детали. Тут важны и настройки оборудования, и квалификация специалиста. Например, один из основных продуктов «Карбонтекса» — преформа для рабочей лопатки вентилятора авиационного двигателя ПД-14. С ткацкого станка она выходит в геометрии готовой детали, так что заказчику не приходится ее дополнительно обрабатывать — достаточно поместить ткань в оснастку, придать нужный изгиб и пропитать смолой. Кстати, на производство одной преформы для лопатки ПД-14 у станка КТ-1000 уходит четыре часа.
Немецкая скорость
Отдельная проблема в 3D-ткачестве — программное обеспечение. До недавнего времени существовала единственная программа, немецкая EAT, позволяющая проектировать тканые конструкции, строя объемную модель из тысяч нитей. Однако лопатку турбины для ПД-14 этот софт даже на мощном компьютере обсчитывал около месяца. В итоге «Карбонтексу» пришлось начать разработку собственной программы. Сейчас ПО находится в стадии доводки, но отдельные модули уже используются — и они при тех же вычислительных мощностях позволяют делать все расчеты на порядок быстрее.
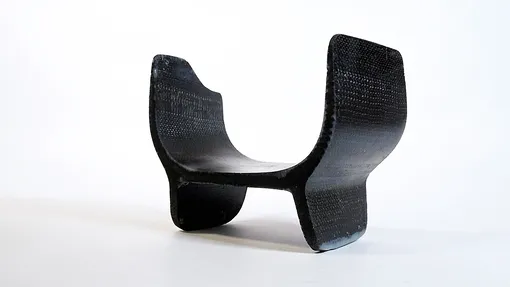
Через тернии к звездам
Из этого рассказа нетрудно сделать вывод, что перед 3D-ткачеством в России открываются головокружительные перспективы. Однако на практике все сложнее. Например, судостроители были бы рады применять композиты нового типа, но отрасль жестко регламентирована. По словам Вячеслава Рогожникова, сертификационные испытания только одной детали обошлись бы в десятки миллионов рублей. Так что на верфях пока продолжают послойно, вручную выкладывать детали из стеклопластика. Есть предприятия, на которых слоистый композит производит автоматика. Они бы тоже с удовольствием перешли на 3D-ткань, но куда девать собственное новое оборудование, в которое вложены немалые средства?
Впрочем, героям нашей истории жаловаться на недостаток заказов не приходится. Чтобы удовлетворить растущий спрос на продукцию, компания «Карбонтекс» сейчас строит дополнительные станки КТ-1000, и загрузить их планируют на все 100%.
Плазма рулит
Сегодня электрореактивные двигатели применяются в основном на спутниках — для маневрирования. Но для смены направления тяги приходится с помощью механических устройств поворачивать либо весь двигатель, либо даже космический аппарат целиком. А это означает не только усложнение конструкции, но и лишнюю массу.
Одним из решений проблемы может стать безэлектродный плазменный агрегат, в котором вектором тяги управляет электромагнитное поле. Устройство такого типа и разработала молодая компания «Эдвансд Пропалшн Системс», резидент Московского инновационного кластера. Пока в фирме работают всего четыре человека, причем трое из них — одногруппники, еще недавно вместе учившиеся в МГТУ им. Баумана. За пять лет компания успела отправить в космос два своих изделия и получить первый коммерческий заказ.
Плюсы и минусы плазменных двигателей
Работа плазменных двигателей, которыми до сих пор массово оснащают такие устройства, основана на эффекте Холла или ионной тяге. В этом случае добиться эффективной векторизации тяги ни на физическом, ни на инженерном уровне не удастся. Раньше на аппараты ставили несколько двигателей, но на распространенных сейчас малых спутниках такое невозможно. Поэтому, как мы уже сказали, холловские и ионные двигатели приходится дополнять механическими устройствами поворота.
Так было до недавнего времени — пока выпускники «Бауманки» не сделали безэлектродный плазменный двигатель с магнитной векторизацией тяги, то есть с изменяемым направлением реактивной струи.
Десять миллиньютонов
Как объяснил Андрей Шумейко, идейный вдохновитель и один из трех основателей компании «Эдвансд Пропалшн Системс», в их двигателе на выходе из ускорителя стоят электромагниты, обмотки которых направлены в разные стороны, под углом к ускорительной оси.
Направление вектора тяги зависит от того, на какой из электромагнитов подан ток. Магнитное поле отклоняется, и поток плазмы следует вдоль его линий. Звучит очень просто, но команда получила уже пять патентов в области плазменных двигателей. В том числе на систему хранения и подачи твердого рабочего тела с возможностью быстрого регулирования расхода, что позволяет снизить объем и массу двигателя.
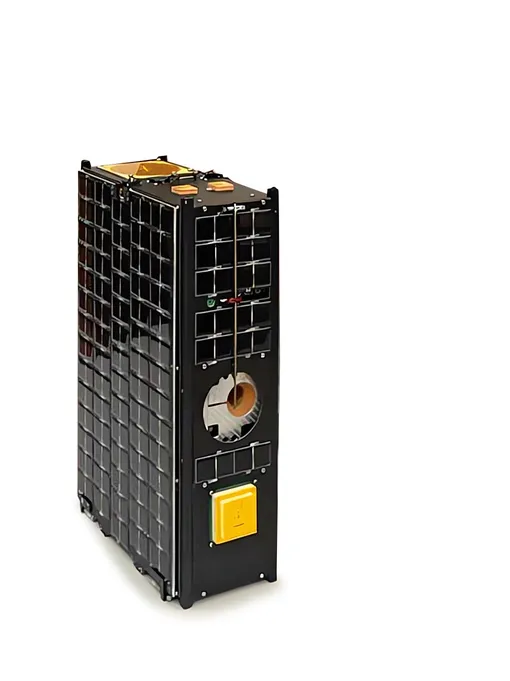
Актуальная версия разработанного устройства, MTVEPT (Electrodeless Plasma Thruster With Magnetic Thrust vectoring), имеет размер 2U (88,1 мм в высоту) и массу до 2,5 кг. Она развивает тягу в 10 мН и может выдавать ее в трех направлениях. Этого достаточно, чтобы перевести спутник размером 6U (200х100х340,5 мм) и массой 12 кг на новую орбиту и позиционировать его нужным образом.
Собрать за девять месяцев
Идея принципиально новой конструкции возникла еще в 2018 году. Тогда Андрей, осваивавший специальность «Электрические ракетные двигатели» в МГТУ им. Баумана, заинтересовался безэлектродными плазменными моделями. В России на тот момент имелись лишь единичные публикации по этой теме, вышедшие в 2007–2008 годах, но будущего инженера вдохновляли работы японского ученого Казунари Такахаши и австралийца Рода Боcвелла.
В 2020 году Андрей Шумейко вместе с двумя одногруппниками зарегистрировал компанию и начал разработку первого двигателя под названием BDEPT (Bi-Directional Electrodeless Plasma Thruster). От текущей версии устройства он отличался принципиально: векторизации удалось достичь за счет того, что в источнике плазмы было несколько отверстий, на каждом из которых стояло по ускорителю.
Параллельно с созданием прототипа ребята подали заявку на финансирование проекта в фонд «Сколково», но в итоге обошлись своими силами. В том же году Андрей уехал учиться в Khalifa University в Абу-Даби и два года посвятил изучению космических систем. Это позволило ему лучше разобраться в принципах работы космического аппарата, особенностях его проектирования и требованиях к двигателям.
В июне 2022 года Шумейко вернулся в Россию и за девять месяцев, к маю 2023-го, команда собрала первый двигатель, который проектировали около двух лет. Тогда же провели цикл наземных испытаний, подготовили интеграцию двигателя со спутником. Детали для аппарата заказывали у индивидуальных предпринимателей, собирали конструкцию сами, а тестировали устройство в лаборатории «Бауманки» — в том числе в вакуумной камере.
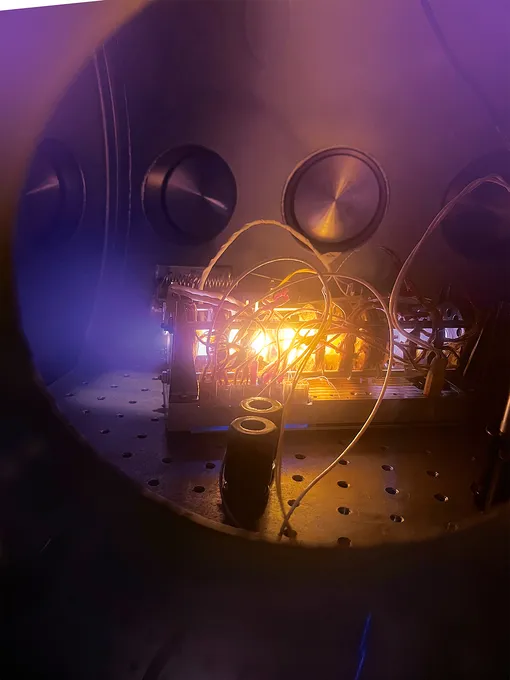
В июне 2023 года BDEPT отправили в космос на борту космического аппарата «Хорс-1» (NORAD ID. 57188). Цикл летных испытаний подтвердил и возможность векторизации тяги при помощи геометрических особенностей газоразрядной камеры, и работоспособность двигателя в целом: он позволил поднять корабль на 250 м относительно базовой орбиты.
В июне запланирован еще один запуск спутника с двигателем нового типа — с тремя векторами тяги и рядом усовершенствований, а в 2026 году в полет должна отправиться версия с шестью векторами. В случае удачи этих экспериментов положение аппарата в будущем можно будет полностью контролировать при помощи ускорителя.
Ну а свой первый коммерческий заказ фирма уже получила — от родного вуза, убедившегося, что конструкция работает.