Эта новая технология становится все более востребованной в промышленности благодаря высокой скорости производства и возможности изготавливать детали различных геометрических форм на одном оборудовании.
Полеты в космос станут безопаснее: ученые создали технологию очистки аддитивных деталей космических аппаратов
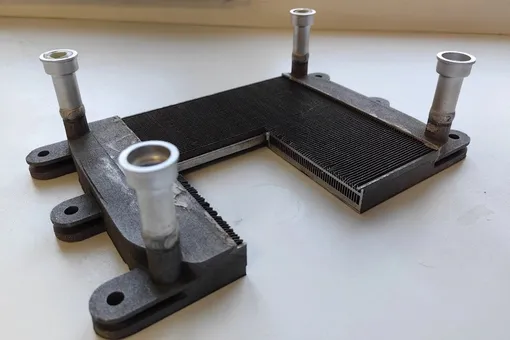
Селективное лазерное сплавление – один методов аддитивного производства, который осуществляется по принципу 3D-печати с помощью лазеров высокой мощности для создания трехмерных физических деталей за счет сплавления металлических порошков лучом лазера.
Однако она имеет и ряд недостатков: поверхность готовых изделий получается слишком шероховатой, также на готовую деталь налипают частицы порошка, поэтому приходится дополнительно ее обрабатывать.
«РКК "Энергия" занялась созданием теплообменников по СЛС-технологии. И столкнулась с проблемой во время испытаний в космосе. Из-за наличия частиц порошка с низкой адгезией к поверхности на внутренних поверхностях теплообменника, система обеспечения теплового режима гораздо быстрее выходила из строя. Это связано с тем, что в процессе работы системы, частицы порошка отрывались от поверхности, что приводило к засорению. Проблема значительно сокращает срок службы системы теплого обеспечения с теплообменниками, полученными селективным лазерным сплавлением, по сравнению с традиционными, которые могут работать 10-15 лет», – рассказала автор работы, аспирантка кафедры № 205 «Технология производства двигателей летательных аппаратов» МАИ Мария Еремкина.
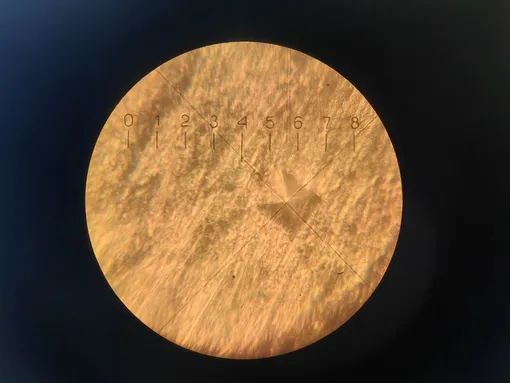
Маёвская технология очистки позволила снизить шероховатость поверхности образцов на 20-25% и очистить поверхность внутренних каналов от налипших частиц порошка. Предложенная методика включает в себя три последовательных этапа химической очистки детали – травление, осветление и матирование.
«Сами по себе эти способы очистки хорошо известны. Образец последовательно помещают в различные растворы на определенное время при повышенной температуре, за счет чего очищается поверхностный слой. Но уникальность нашей работы в том, что их раньше не применяли для деталей, полученных селективным лазерным сплавлением. Мы сумели подобрать оригинальные химические составы с оптимальной концентрацией. Также мы на практике определили, сколько времени держать образцы в растворе. Это важно, потому что, если их передержать, поверхность начинает деградировать с существенной потерей массы», – подчеркнула Мария Еремкина.
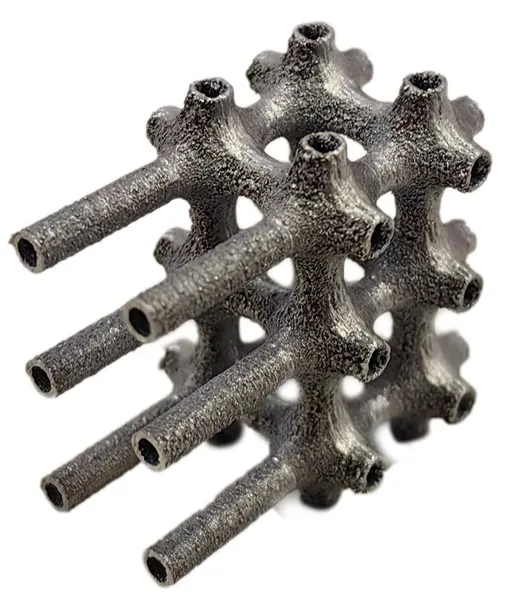
Для исключения коррозии деталей после такой трехэтапной очистки ученые предложили защитить поверхность нанесением химического никель-фосфорного покрытия. Результаты эксперимента показали положительный результат – на поверхность внутренних каналов было осаждено никель-фосфорное покрытие с толщиной слоя 8-10 мкм: оно характеризуется повышенной коррозионной и износостойкостью, повышенными физико-химическими характеристиками.
Помимо РКК «Энергия», интерес к разработке проявили в Центральном институте авиационного моторостроения им. П.И. Баранова (ЦИАМ). Они передали специалистам МАИ для исследований образцы теплообменников собственного производства. Сейчас работа ученых по повышению долговечности готовых изделий продолжается.